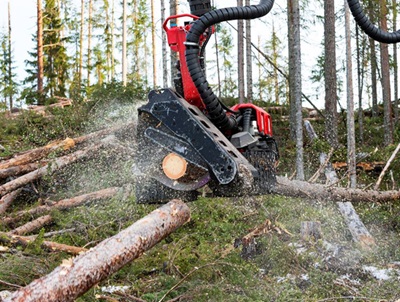
The 2024 improvement includes an upgraded length-measuring function.
The Komatsu S172 has an upgraded length-measuring function as well as improvements that will increase the reliability and performance of the head. Several improvements have been made to the length measuring function to increase the measuring accuracy. For example, the measuring wheel arm now has a stronger design, which improves its service life and allows it to better withstand pressure from the measuring cylinder. Other improvements include the measuring wheel cylinder and reinforcements in the frame. These improvements allow the measuring wheel to better follow the contour of the stem, increasing measurement accuracy.
Another area of improvement is the saw unit, which has a more robust saw bar holder. This provides a smoother and more reliable operation. The saw unit has also been equipped with a protective plate that covers the saw bar holder and protects the chain when the saw bar is in the starting position.
Other new features include an optional hydraulic top knife, which is ideal for cutting crooked stems or thick and difficult-to-handle branches. The head has also been improved with reinforcements in the frame, stronger attachment of the head computer and the use of expander bolts for the feed wheel arms. All these improvements help to increase the reliability and lifespan of the head. Source
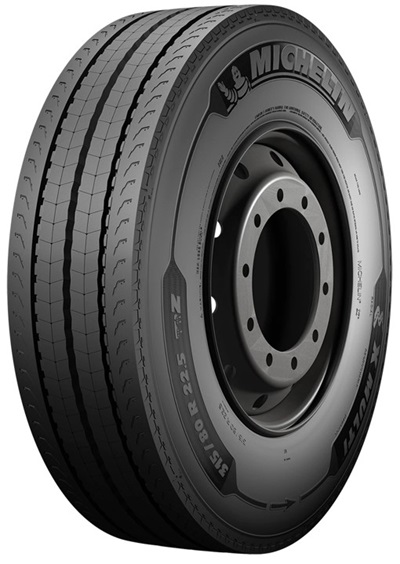
Michelin debunks the myths about today’s modern, safe and reliable retreads.
These tyred retread myths are rooted in outdated information still circulating from decades ago when truckers attributed all road gators to retreads. Some of these same old-school truckers also checked their tyre pressure with a tyre thumper. In addition, the truck tyre retread industry has been impacted by a surge of ultra-low-cost imports that are 65% less likely to be re-treaded, are worse for the environment and add to the misconceptions about retreads. Fortunately, these misconceptions are changing, and most major truck fleets and business savvy owneroperators are on board with retreads.
- MYTH 1: Buying low-cost import tyres will save more money than retreading premium tyres. Truth: Successful fleets that buy premium tyres and have adopted retreads don’t believe this myth. Eighty-nine percent of fleets with 500 or more trucks use high-quality tyres with multiple re-treaded lives. These fleets carefully track their cost per mile and total cost of ownership, and they see that retreads are clear winners for them. Retreading a premium tyre two times can deliver 500% more miles per tyre than an ultra-low-cost new tyre. The cost of each re-treaded tyre compared to a premium new tyre is generally 50% less.
- MYTH 2: All the rubber on the side of the highway comes from retreads. Truth: New and re-treaded tyres fail at the same rate.
- MYTH 3: Retreads are not safe and can cause accidents. Truth: Re-treaded tyres are so safe that on any given day, 80% of commercial aircraft are landing on re-treaded tyres.
- MYTH 4: Retreads are less fuel efficient than new tyres. Truth: Many manufacturers offer the same low-rolling resistance tread designs on their new and re-treaded tyres while independent re-treaders can also offer several low-rolling resistance options.
- MYTH 5: Retreads don’t do well in extreme temperatures. Truth: Improper maintenance and tyre inflation lead to failure, especially in extreme temperatures.
- MYTH 6: They don’t look as cool as new tyres. Truth: This may once have been true, but today’s innovative retread processes and options for custom painting make it hard to differentiate new tyres from re-treaded ones.
- MYTH 7: Retreads are not as good for the environment. Truth: Manufacturing a re-treaded tyre requires 15 gallons less oil and approximately 90-100 pounds less total material than a new tyre. Source
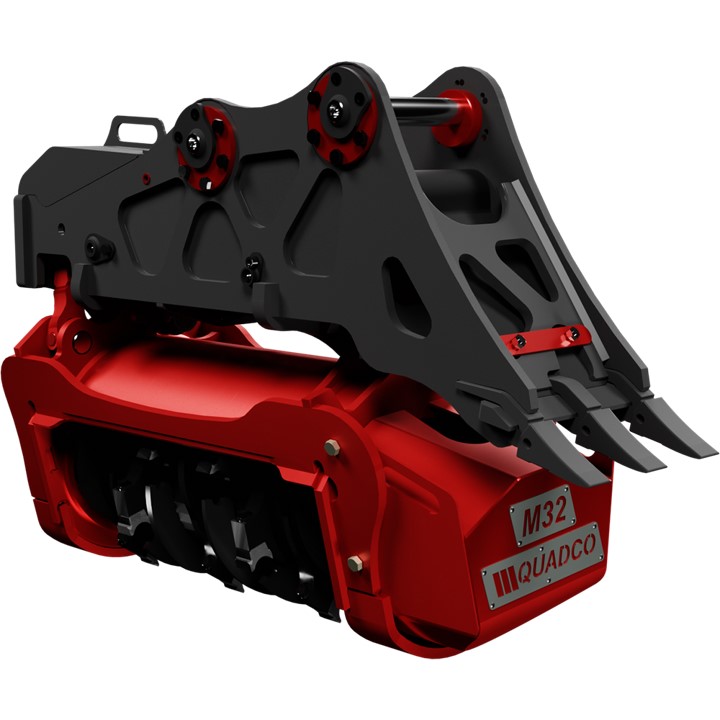
The 32QDM is compact without compromising on toughness.
Since their beginning as a small forestry equipment manufacturing shop in 1989, Quadco have built their reputation on a single promise: to never compromise on quality or service. That means listening to customers and dealers to get their feedback on the products’ ability to withstand heavy applications on the job site – and adjusting designs accordingly. That’s how the newest addition to Quadco’s line of forestry mulchers was born. The brand new Quadco 32-inch Drum Mulcher (32QDM) pairs innovation with value to offer forestry professionals , versatile solution for tree and brush clearing.
As the latest addition to Quadco’s line of rugged forestry mulching attachments, the 32QDM is compact, without compromising on toughness. It is designed to run on 8 to 15 ton excavators. Rather than offering a lateral tilt as a costly add-on feature, the 32QDM comes with a 100-degree lateral tilt as standard. This attachment also features a spiralized drum to help distribute material evenly over the cutters and serve as a bite limiter. The 32QDM is compatible with a variety of Quadco teeth and includes a fixed heel with replaceable bucket teeth for added productivity.
Like all Quadco attachments, 32QDM is built to stand the test of time and perform like new after years of heavy duty applications. Manufactured especially for professional contractors, 32QDM features a built-in universal boom adapter to provide equipment dealers and rental fleets with the flexibility they require to meet the needs of their clients. Changing carriers is as simple as replacing the pins and sleeves, saving you valuable time and money. Source
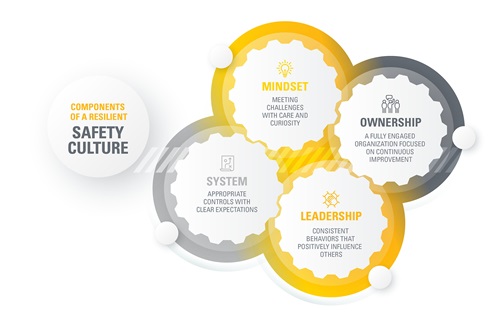
Caterpillar Safety Services incorporates the latest research and approaches to address safety excellence within organizations.
With safety no longer being a box-ticking exercise but a true measure of employee engagement, Caterpillar Safety Services helps build a strong culture where safety practices are embedded across an organization. Today, Caterpillar Safety Services assists companies with improving the four components of a resilient safety culture, where safety is approached proactively, and all team members take ownership of safety. The components include:
- System – clearly defined safety expectations embedded in policies and procedures to identify and mitigate risk.
- Mindset – a shared mindset that safety is everyone’s responsibility, people make mistakes and an environment of openness that makes people feel safe to speak up.
- Leadership – specific, consistent leadership behaviours at all levels of the organization that positively influence people toward safe work.
- Ownership – occurs when all levels fully engage in the creation and continuous improvement of the safety system.
Caterpillar Safety Services recently launched two updates to its programs contributing to resilient safety cultures: an updated Safety Perception Survey and a program focused on human and organizational performance.
Firstly, the Caterpillar Safety Services Safety Perception Survey analyses an organization's safety culture. Building on 35 years of research and study, the new Safety Perception Survey updates language and modern concepts of safety culture excellence, adding questions related to psychological safety and human and organizational performance.
Secondly, human and organizational performance is a framework concept for talking about safety and creating a resilient safety culture. It’s a mindset that allows organizations to build more error-tolerant systems by teaching leaders that expecting perfection from workers, processes, or procedures is not realistic.
Using human and organizational performance principles, Caterpillar Safety Services applies a new understanding of human behaviour to safety. Leaders create an environment where employees feel empowered to speak up to share their ideas, struggles and mistakes. The organization learns to improve its safety system continuously. Through recognition of workers’ positive contributions, they want to be more involved, resulting in a more engaged and proactive safety culture with improvements in morale, retention, efficiency, and profitability.
Caterpillar Safety Services assists organizations with implementation of human and organizational performance principles through its Leadership Development and Coaching program. Tailored to the specific needs and objectives of the individual leaders, the program includes a mix of workshops, assessments and individual face-to-face sessions. It helps each leader understand their strengths and areas for development in safety management, demonstrates how a leader impacts the safety culture, and creates personalized development plans for all leaders that align with organizational goals and processes. Source
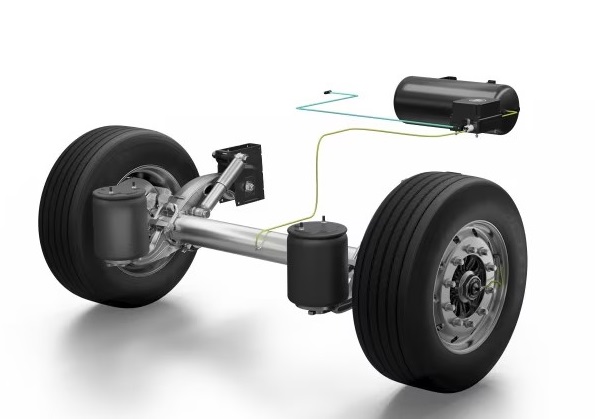
BPW explains why the potential cost savings from automatic control of tyre pressure.
Margins in the transport sector are getting smaller and smaller. This means anything that tangibly reduces transport costs will relieve the pressure on the transport company's balance sheet. In this context, it is astonishing that in Germany alone, millions of litres of excess diesel are consumed every year in road freight transport, unnecessarily emitting CO2 into the atmosphere, and that vast quantities of tyres wear out prematurely. The main drivers for this are pressure variations in the tyres, which cause a considerable increase in fuel consumption and wear on the trailer. This is not a coincidence, as truck tyres have to take a lot of punishment: constantly changing load weights, road conditions and temperatures quickly lead to pressure variations, causing the tyres to wear out at a rapid pace. This not only increases operating costs, but also the risk of accidents: after all, tyres are the only point of contact between the trailer and the road, and even slight variations in pressure can jeopardise driving stability. A puncture can cause serious accidents that may endanger cargo, the vehicle or other road users. According to ADAC TruckService, most truck accidents are caused by poor maintenance. In accordance with this report, breakdown service staff are called out about 40,000 times per year. According to their own data, punctures are the cause in two thirds of the cases, i.e. 26,400 potentially prematurely worn tyres that can also no longer be retreaded. A new premium-brand trailer tyre easily costs 300 euros and more.
If you want to avoid unplanned downtime due to loss of tyre pressure, tyre pressure control systems are a suitable solution. Because after all, a warning signal alone does not eliminate the pressure variation. Anyone familiar with the realities of day-to-day transport operations knows that some responsible persons will ignore warnings in the driver's cab in order to meet deadlines. This is why BPW give the recommendation: monitoring is good, regulation is better.
A tyre pressure control system such as the award-winning AirSave from BPW compensates for a pressure variation of more than five per cent within ten minutes. Fully automatically, without interruption of the transport process. In the event of a puncture, the system pumps powerfully to compensate for the flat tyre – so the driver can safely reach the workshop and avoid unplanned downtimes.
AirSave also reduces the economic burden on fleet operators, here is an example: for a three-axle vehicle with a mileage of 120,000 kilometres per year and an average pressure deviation of 10 per cent, the system delivers a cost benefit of 700 euros per year – solely as a result of the fuel savings (around 250 litres) and the longer service life of the tyres.
But what about existing vehicles? AirSave will also be available as a retrofit solution from the end of 2024. Retrofitting AirSave is especially worthwhile for trailers with particularly valuable superstructures such as tank silo vehicles or vehicles for transporting hazardous goods. For large fleets with more than 200 vehicles, a combination of AirSave and telematics is practically indispensable: the savings in terms of economy, time and organisation effort cannot be disregarded by any business-minded fleet operator.
So simple tyre pressure monitoring systems have their place in the market. Nevertheless, it is to be expected that automatic tyre pressure regulation using intelligent TPR systems such as AirSave will soon become the standard in the transport industry due to the many additional benefits, such as the avoidance of unplanned downtimes Source
New Eco Log dealer in Canada
Eco Log is proud to announce IDM as our new Dealer in Canada, a company dedicated to forestry that will provide the Canadian market with Eco Log machines, service and support ahead. Take the opportunity to visit them at the Atlantic Heavy Equipment Show in Moncton, March 27 & 28, and take a look at Eco Log´s machines and talk to the representatives from the Eco Log Team on site. Source
Scania accelerates deployment of autonomous hub-to-hub transport
Scania’s programme launch comes as customers look for trusted and reliable partners for developing and deploying autonomous vehicles within their own operations. This new solution stands out due to its adaptability to customers’ specific routes and transport profiles. Scania is expanding its strategic development of autonomous hub-to-hub transport solutions, with the launch of an Autonomous Commercial Pilot Programme. As part of TRATON Group, Scania will also be involved in a new partnership with US-based Plus, which will integrate its Level 4, fully autonomous SuperDrive™ technology stack into Scania and TRATON Group vehicles. Source
Read MoreTo see the full list of international logging, roading and trucking conferences and expo’s, please click the “Events” tab at the top of the page.
Read More