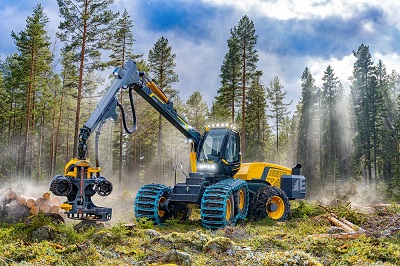
And along with it - the G-series wheeled harvesters.
The G-series pendulum arm harvesters includes the models 550, 560, 580 and 590. The new Eco Log 580G has now raised to yet another level and shares the same platform as Eco Log 590, which means it is an even stronger machine than before. During the fall, Eco Log introduced several, large updates on the pendulum harvesters – from a new control system, new rear wheel transmission and anti-spin system to a simplified hydraulic system and several improvements regarding serviceability and safety through improved access. All of these updates are now implemented on the new G-series.
The new spacious cabin has ample storage possibilities. The swivel seat enables you to easily access and use the rear cab section. The cab boasts windows made of thick safety glass and secure access routes via a brand new platform that allows you to enter and exit your cab via the side-mounted door both easily and safely.
The cab uses a brand-new approach for the heating, ventilation and air conditioning (HVAC) system. The system has automatic temperature regulation and has been thoroughly tested in both hot and cold climates. The interior is modern and well thought out. It offers, amongst others, plenty of space, several smart storage possibilities and broad charging options with multiple connections.
All G series harvesters are equipped with Eco Log’s NexSci control system, user-friendly keypads, an eleven-button joystick, and a new sound system with integrated subwoofer that is compatible with both Apple CarPlay and Android Auto. The interior of the cabin also has effective sound insulation and comfortable lighting in the shape of integrated LED lamps. Several options for work lightning at the front as well as rear side of the cabin. Source
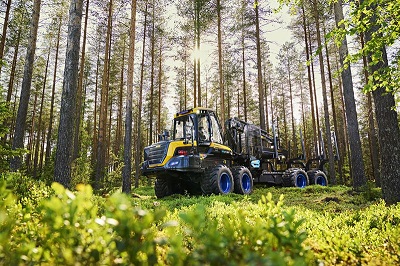
SSAB have joined forces with Ponsse to deliver fossil-free steel to Ponsse from 2026.
This partnership will further solidify Ponsse’s position as a provider of sustainable forest machines and bring SSAB closer to its goal of establishing a fossil-free value chain. Joint efforts are needed to meet the challenging CO2 reduction targets in forest machines. Both companies prioritize sustainable solutions and will strive to make a positive impact on forest machines using SSAB Fossil-free™ steel, fostering innovation while respecting nature.
SSAB’s products and services will play an important role in assisting their customers in achieving their climate objectives during the transition to a low-carbon economy. The Ponsse EV1 forwarder concept with completely electric drive and their partnership with SSAB regarding fossil-free steels will lead their development towards carbon neutral forestry.
SSAB plans to revolutionize the entire steelmaking process. SSAB aims to deliver fossil-free steel to the market at a commercial scale during 2026 and to largely eliminate carbon dioxide emissions from their operations in around 2030. SSAB works with iron ore producer LKAB and energy company Vattenfall as part of the HYBRIT initiative to develop a value chain for fossil-free iron- and steelmaking, replacing the coking coal traditionally used for iron ore-based steelmaking with fossil-free electricity and hydrogen. This process virtually eliminates carbon dioxide-emissions in steel production. Source
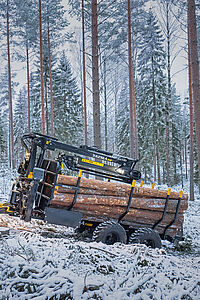
Nate Drive (ND) is intended for longer and more demanding use.
Kesla Oyj is a Finnish manufacturer of truck cranes, logging equipment as well as tractor-based forest technology and material handling equipment with long and traditional roots, especially as a manufacturer of tractor-based machinery, since the 1960s. Now, the company is also launching a strong nave drive for the smallest forest trailers of 10 tonnes.
The Kesla 114 is the smallest trailer in the Kesla forest trailer range and has a load capacity of 10 tonnes. Previously only available with a hydraulic roller drive (HD), the trailer model is now available in both an H version (unpowered, with the option to retrofit HD) and an ND version (with nave drive).
The tyres of a nave-driven trailer can be fitted with chains. ND means strong nave drive. While HD is intended for occasional use and lighter traction needs, ND is intended for longer, more demanding use. The traction motors of the Kesla 114ND trailer come on the rear wheels. The 114ND trailer’s nave drive is designed with mid-size tractors in mind, and even 70 l/min at 190 bar gives good traction.
The drive system is linked to a differential gear lock, which is constantly on. The differential gear ensures the rotation of both wheels, thus ensuring good traction. The 114ND trailer has a maximum drive power of 1.6 tonnes and a maximum speed of 5 km/h. In the roller drive, the corresponding figures are 1.4 tonnes and 2 km/h. The nave drive is controlled by the tractor’s hydraulics, but a drive valve for electric traction control is coming to the market in the autumn.
The Kesla 114ND trailer has the 500/50R17 tyres and the high-traction rear tyres can also be fitted with chains. In addition, the 114ND is available with a wide range of equipment, including forwarder-type bunks. The H model can be retrofitted with a roller drive. Source
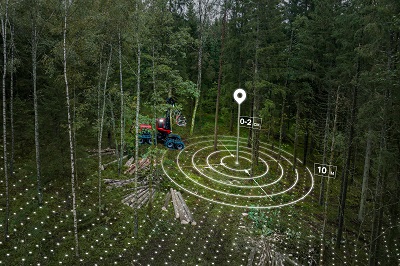
This provides the foundation for a new and exciting function, Precision.
Digital developments unfold at a fast pace, and for forestry this means opportunities for new, smarter ways of working. Thanks to developments in the satellite positioning technology GNSS, MaxiFleet, Komatsu Forest fleet management system, can now show the machine’s position within just a few centimetres, providing the foundation for a new and exciting function, Precision.
GPS positioning has long been used in forestry and has helped in the development of work methods, facilitated collaboration, and increased productivity. However, an error margin of 0 to 10 m (0 – 33 ft) has meant fairly inaccurate positioning. Today’s new RTK GNSS technology enables positioning with an error margin of just a few centimetres, paving the way for countless possibilities and even heralding a paradigm shift to a smarter forestry.
One new feature is that the operator can use geofencing – a digital fence that is added when planning an area. This could be around a harvesting area or to mark protected areas such as ancient monuments or charcoal pile remains. This feature means greater peace of mind for forest owners and operators alike as it indicates more clearly where the operator should harvest and the areas they should avoid. Geofences can also be linked to alarms to warn the operator when the machine or the crane tip is approaching such a boundary.
Since the machine’s position can be determined with great precision, the user can also see the machine in the map program – including the direction of the crane and the location of the crane tip. This extreme precision enhances the practical usability of the map layer data for the operator. Another advantage of the new technology is that the machine’s route is plotted with significantly better accuracy, making the planning more effective.
In MaxiFleet the operators have always been able to see where a tree was felled, but with the greater precision now available, the exact position of each felled log can be shown. This lets the operator know exactly where the timber is located, even in the dark or when covered with snow. This will also make it easier to see the assortment found in each log pile or at the roadside.
Another new function is stem code visualization, which means that individual stems can be visualized using stem codes based on, for example, biodiversity considerations. Stem coding supports the operator in their work, enabling them to make better decisions more easily and making it easier to follow directives, such as for the distance between future trees. Based on previously coded trees, MaxiFleet can also suggest when it is time to cut a high stump or leave a tree standing, making the operators work easier. It can also keep track of the number of high stumps, meaning one less thing for you to worry about.
The GNSS system uses several satellite systems to determine positions. This refinement has been enabled by the arrival of several new satellites, including the commissioning of Galileo, the European GNSS system.
Accurate positioning using satellite data requires more known measurement points to help correct the satellite’s signals. Previous technology has been based on only the machine having a signal receiver, but thanks to networked RTK (real-time kinematic), the machine now has access to several fixed reference stations. These are used to correct any errors in the satellite signals, thereby improving positioning precision from several meters to a few centimetres. Source
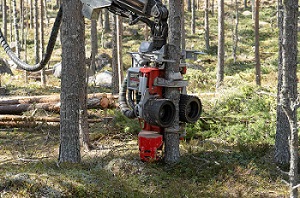
The head provides a balance between flexibility, capacity and durability.
The new 318 MK2 saw unit of the 5000V will make work easier. The need for maintenance will be minimised, and durability will increase. The changes make it easy to change the bar, maintain the saw unit easily, and increase the durability to its maximum. The 5000V measurement unit has received mechanical, electronic and hydraulic updates. The construction of the measuring wheel cylinder is updated, the hydraulic circuit is new, the measuring wheel arm and its attachment are reinforced, there is a new contactless encoder in the measuring wheel, and two conical roller bearings that are lubricated from the outside. Altogether, the changes will allow the measuring wheel to follow the contour of the stem even better and provide the best measurement result.
The contour of the saw box is changed, and the position of the saw unit has been optimized to handle trees with larger root bones and thus increase production significantly. The saw box also has a root bone plate to protect the chain and bar. The saw box has also been extended and is now adapted for saw bars of 82 cm (32 in). The new 5000V easily handles large trees, both when felling and processing. The maximum cutting diameter is 74 cm (29 in).
The Log Max 5000V has new feed roller motors with hoses without banjo fittings. The new engines are of a high-flow model with increased efficiency, generating better performance for the harvesting head. The changes provide a better and higher flow, which reduces heat development and thus reduces energy losses. It also increases the unit's feed speed. The feed wheel arms have also received an updated design to be able to process both coarse and thin logs better.
The hoses for the multi-stemming unit and the rotator control are on the left side of the felling link at 5000V. The updates make the hoses run inside the protective bar, less exposed and will make them last longer. The attachment for the hoses for stump treatment and grease lubrication also has a new design, which means that the hoses are exposed to minimal wear and have increased durability.
To simplify service, facilitate transport and increase safety, a "Safety Pin" has replaced the safety chain, which forms a locking mechanism between the frame and the felling link. One can now link a bracket under the rotator to a stand in the frame with the help of a locking pin. To increase durability and productivity, the frame construction of the 5000V has received several updates. In order for all lubrication to be done when the head is in the tilted position, the head has accessible lubrication points. The lubrication points are brought forward on the saw box so that they are easy to get at. It increases safety, facilitates maintenance work, and shortens downtime.
To improve the frame’s durability and life span, Log Max have changed the design of the measuring wheel hole. We also reinforced the stoppers for the roller arms, when in the closed position, at the inside of the frame to increase the frame’s strength and stability. To increase durability and reduce the risk of cracks in the frame, Log Max have created a reinforced attachment for the upper delimbing knife. The frame is reinforced at the mainline, where the upper delimbing knife slides on the frame to increase durability and extend its life span. Source
LEVITOI project creates research data that will enable more soil-friendly tires
Coordinated by the Oulu University of Applied Sciences and funded by Business Finland, the LEVITOI project brings together several companies in search of solutions for safer and less soil-compacting machine work on soft surfaces. Nokian Heavy Tyres is the leading company in the project, and the research has already produced promising results for enabling e.g. tires that monitor the driving surface properties. Source
JCB is introducing its first full electric wheeled loader
JCB is expanding its full electric equipment line-up, with the launch of the 403E wheeled loader, helping customers to meet the challenge of carbon reduction on site. The machine is powered by a 20kWh lithium-ion battery pack, assembled from proven JCB modules, as pioneered in the company’s existing range of electric equipment. These batteries, coupled with high efficiency electric motors and optimised traction and hydraulic systems, deliver class-leading performance, with the loader capable of completing a full working day, or 4-5 hours of continuous use in a mixed duty cycle. Source
Read More“Workability and productivity among CTL machine operators – associations with sleep, fitness, and shift work”
International Journal of Forest Engineering, 2023. Heli Kymäläinen, Teppo Hujala, Carola Häggström & Jukka Malinen. Source
“A framework for defining weights of decision makers in group decision-making, using consistency between different multicriteria weighting methods”
International Journal of Forest Engineering, 2023. Boško Blagojević, Eva-Maria Nordström & Ola Lindroos. Source
Read MoreTo see the full list of international logging, roading and trucking conferences and expo’s, please click the “read more” tab.
Read More