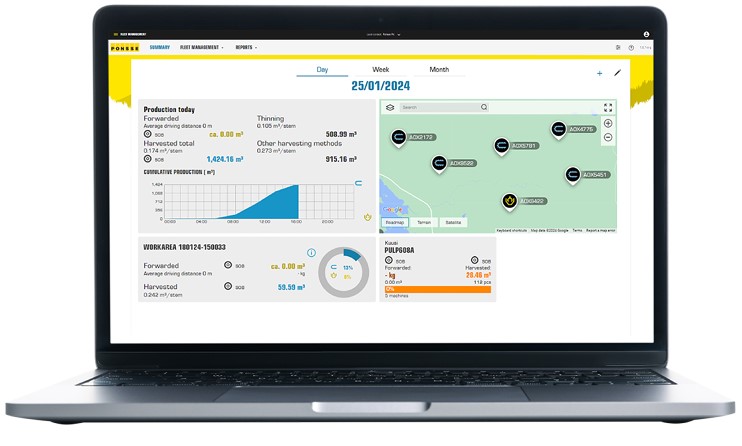
It is a digital service platform and forest machine management system.
Ponsse Manager 2.0 provides customers valuable data of machines’ location, productivity figures and fuel consumption, among others. The Ponsse Manager monitors the progress of stands, plans, and manages machine transportation, keep track of machine outputs according to assortment and print out measuring certificates.
With the quick tempo of the modern world and the huge amount of data we see every day, finding the correct piece of information is often like trying to find a needle in the haystack. The new Ponsse Manager is a completely new approach to more sustainable and more digitalized forestry. All the development has been based on customer feedback and customer needs from all over the world.
In Ponsse Manager 2.0, the user can create a personalized home page focusing on the most important data. Every important information is visible immediately, variations can be discovered quickly, and corrective action can be taken directly. With the single sign-on, all digital solutions required to improve operational efficiency and productivity are at the user’s disposal in one web address. Ponsse Manager keeps customers up to date on data that affects their machines' profitability and helps improve operations' efficiency.
One of the new key features is the possibility to download all reports and, e.g. combine them in a spreadsheet with other data to create new valuable views of your operations. Mobile applications will also be available to download for free from your app store. “The mobile app is easy to use on site, with all required functionalities available for professionals working in different roles” says Jenni Pulkkinen, Product Owner Digital Solutions.
Ponsse is developing its digital solutions together with its customers. The digital innovations address the right issues and provide relevant support for both professionals working on-site and those responsible for smooth and efficient fleet management. Source
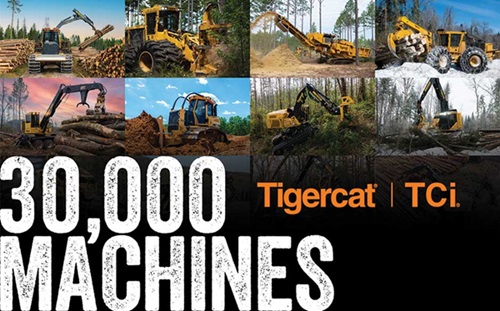
In just over 30 years in business, Tigercat Industries has shipped its 30,000th machine.
Tigercat Industries is pleased to announce that it has built and shipped its 30,000th machine in January 2024, just over 30 years into its existence. From humble beginnings in 1992 when Tigercat had a single product, very little dealer representation, and produced just a handful of machines, the company has grown steadily, expanding both its production capacity and product breadth.
A few quick facts
- Tigercat debuted the 726 feller buncher in April 1992 at a forestry equipment show in Quitman Georgia.
- By 1995, Tigercat had two drive-to-tree feller bunchers, two track feller bunchers, and two bunching shear models with distribution in Canada and the United States.
- By 1997, Tigercat had a full product line to offer southern US dealers with the addition of a knuckleboom loader and the industry's first successful, serial production hydrostatic skidder.
- In 2000, Tigercat was well on its way to becoming the dominant player in steep slope harvesting applications, offering a six-wheel drive skidder and the L830 feller buncher. Both were destined to become flagship products for the company. In addition, Tigercat entered the vegetation management sector with its first mulcher carrier. The range of carriers and attachments that have followed are crucial inputs to wildfire mitigation strategies in many regions globally.
- By 2005, Tigercat was present in Chile, Brazil, Uruguay, Australia, New Zealand, South Africa, UK and Sweden among other countries.
- In 2012 Tigercat had grown in 20 years from two to 1,000 employees and introduced the 880 logger, the first in a series of versatile, forest duty swing machines.
- Today, Tigercat has the most complete full-tree product line-up in the industry, along with a growing range of CTL harvesters, forwarders and harvesting heads. Tigercat launched a new brand, TCi in 2022 and put the TCi badge on its first dozer, the 920. In the last four years, the company has been developing a line of material processing products with two launches to date – the 6500 chipper and 6900 grinder. 2024 will see a slew of new and exciting products introduced to the market.
Tigercat recently opened a new facility dedicated to the material processing product line and is currently building an additional facility. When complete the company will have over 1.4 million ft2 (130,000 m2) of manufacturing capacity. That's 130,000 m2 or 32 acres under roof. Over 160 dealer locations in 25 countries represent the Tigercat and TCi brands, along with an extensive factory support network. The company employs over 2,000 people. Source
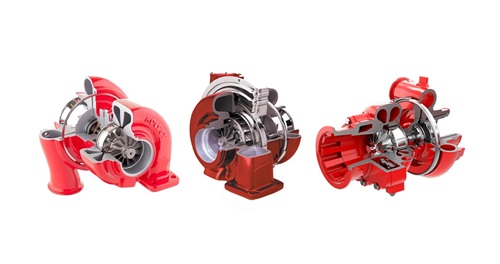
Turbochargers are critical components used for optimizing performance of on-highway and off-highway engines.
They increase engine power, improve fuel efficiency, and help reduce emissions of internal combustion engines (ICE). Cummins producers a range of turbochargers to support a wide variety of engine requirements used in countless applications and explain the types of turbochargers to us.
The primary types of turbochargers are Fixed Geometry Turbochargers, Wastegate Turbochargers and Variable Geometry Turbochargers. Engine manufactures consider several factors when choosing the type of turbocharger that is best for their engine and application.
Turbochargers increase air flow to the engine cylinders, allowing for greater power density of the engine which improves combustion. Turbochargers use the energy in the engine exhaust gas to rotate a turbine at high speeds. A shaft connects the turbine wheel to a compressor wheel. The rotating compressor increases the pressure and flow of fresh air to the engine.
The differences between the types of turbochargers described in this article are based on how the exhaust gas is manipulated before it reaches the turbine wheel.
- Fixed Geometry Turbochargers: The exhaust gas flows through the turbocharger turbine housing before reaching the turbine wheel. A cavity in the turbine housing is called the volute. With Fixed Geometry Turbochargers, 100% of the exhaust gas flows through the volute to the turbine wheel. The wheel of the turbine and the shape of the volute affect the turbocharger and the engine performance. The turbine housing and wheel geometries are designed to optimize performance across various engine speeds and loads. Some Fixed Geometry Turbochargers also include a nozzle with fixed vanes to improve turbine performance at specific operating conditions. The advantages of Fixed Geometry Turbochargers, compared to the other designs, are the simplicity of the design, low cost and smaller size. The main disadvantage is the lack of flexibility in optimizing engine performance. Given its fixed geometry, compromises must be made between optimal engine transient response, peak torque capability, and engine rated speed and power. Fixed Geometry Turbochargers are often used in engines that operate at a constant engine speed. This includes engines used in power generation and large industrial and marine applications. Fixed geometry turbochargers are rarely used in on-highway applications.
- Wastegate Turbochargers: A Wastegate Turbocharger is similar to a Fixed Geometry Turbocharger with an added feature in the turbine housing: a wastegate valve. When the valve is open, a portion of the exhaust gas by-passes the turbine wheel and reduces its speed. This helps regulate airflow from the compressor to the engine. With Wastegate Turbochargers, a smaller turbine housing can be selected to increase air flow to the engine at low engine speeds. This improves engine response and vehicle acceleration. The wastegate valve is then opened at higher engine speeds to prevent over boosting the engine and to prevent the turbocharger from exceeding its rotational speed limit. Compared to Fixed Geometry Turbochargers, a big benefit for Wastegate Turbochargers is that they offer more flexibility in optimizing engine performance. One of the challenges is that Wastegate turbochargers are slightly more expensive and are larger in size due to the addition of an actuator (a component that produces force or torque) to operate the wastegate valve. Actuators may be either pneumatic (mechanical) or electric. Wastegate Turbochargers are primarily used in applications that operate at varying engine speeds and loads. These engines are used in a variety on-highway and off-highway applications.
- Variable Geometry Turbochargers: Variable Geometry Turbochargers are more complex than Fixed Geometry and Wastegate Turbochargers. Variable Geometry Turbochargers work by varying the area of the exhaust passage immediately before the exhaust gas enters the turbine wheel. Reducing the area increases the pressure and the velocity of the exhaust gas entering the turbine wheel. This in turn increases boost pressure and air flow to the engine when desired. Heady-duty trucks that operate in diverse environments with varying loads can be a great example where the benefits of the Variable Geometry Turbocharger can help. Variable Geometry Turbochargers can be more expensive than other types of turbochargers. While they are expensive, Variable Geometry Turbochargers do offer the benefit of significant optimization of engine performance across a wide range of engine speeds and loads. These turbochargers can also be used to enhance engine braking, drive exhaust gas recirculation and support exhaust aftertreatment thermal management. Variable Geometry Turbochargers are used on a wide variety of applications to help meet the most stringent emissions regulations. They are primarily found in on-highway and off-highway applications with varying engine speeds and loads because they help ensure optimized performance across many applications and duty cycles.
Engine manufacturers consider various trade-offs when choosing turbochargers and air handling architectures. Some engines use a single turbocharger while others use more than one turbocharger arranged in a series or in parallel configurations.
Cummins offers a range of turbocharger products to meet our customer’s needs. In addition to designing turbochargers for diesel engines, Cummins is a technology leader in turbochargers for alternative fuels, including natural gas and hydrogen. Reach out to us to know more about our products. Source
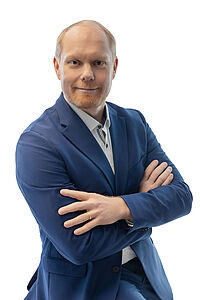
Nieminen will assume his new position no later than August 2024.
The Board of Directors of Kesla Oyj has appointed Pasi Nieminen (Master of Science in Production Engineering, born 1975) as the CEO of Kesla. Nieminen will join Kesla from Toyota Material Handling Europe, where he has worked in management position of the company's SAP Transformation Program in Europe. Prior to that, Nieminen served as Managing Director of Toyota Material Handling Finland for over ten years, before which he worked in various positions within the technology industry.
In line with its strategy, Kesla focuses on profitable growth in all its three business areas: tractor attachments, truck and industrial cranes, and logging equipment. Growing beyond the company’s current size requires deep expertise in implementing an innovative business and transformation strategy and experience in mechanical engineering business as well as production management.
A skilled staff, deep industry expertise, flexible production, competitive products, a strong brand and partner network as well as high customer satisfaction are inherent characteristics of Kesla.
The Board of Directors of Kesla Oyj appointed CFO Ilkka Miettinen as the company’s interim CEO starting from 2 November 2023. Once Nieminen assumes his position, Miettinen will continue as the company’s CFO. Source
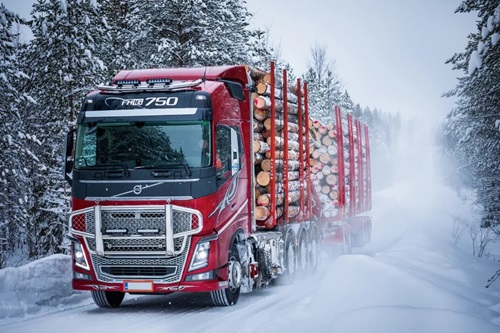
This all-season classic, commonly used for timber transport, has been improved.
For decades, Nokian Tyres Noktop 21's traction, self-cleaning properties and versatility on challenging surfaces has made it the trusted go-to traction tread for commercial use. From the beginning of 2024, the classic tread gets new features – while keeping its first-class properties.
From February 2024, Noktop 21 gets a new look and new features. While the time-proven rubber compound, tread pattern and two-layer Cap/Base structure remain, it now has broader width range of 240 to 280 mm (9.4 to 11 in), added stud holes for every width, clear product markings for identification as well as 3PMSF marking as proof of safe winter use.
By creating new molds and adding some improvements, Nokian gave the classic tread a fresh start. With the new 280 mm (11 in) width, the Noktop 21 range covers the most popular tire sizes very well. Over the years, the Noktop 21 drive tread has become something of a legend in the transport industry. Its good self-cleaning properties and remarkable traction have earned the trust of people working on wintry roads. Its tread pattern has also been copied by many other manufacturers.
Earlier versions of the Noktop 21 tread had a distinctive white stripe, which Nokian later had to leave out for manufacturing reasons. Now, the renewed Noktop 21 has clear markings with model number, country of origin and winter symbols.
Retreading makes sense – both economically and for the environment. Particularly in the Nordic countries most heavy tires get a second round of use with quality retreading. For all-season general use, you cannot beat the two-layer Cap/Base structure of the original Noktop 21. The tread profile changes over the winter to become suitable for summer use. And with the new molds and features, the Noktop 21’s success continues. Source
District Manager Promotion for Tigercat product support representative
Tigercat Industries is pleased to announce that Aaron Piper has accepted a new position as district manager for the states of North Carolina and Virginia. Already a familiar face to Tigercat dealers and end users in the region, Aaron is based in Sunbury, North Carolina and has played a key role as a Tigercat product support representative (PSR) for the past nine years. He will remain heavily involved in product support and will expand his role with district manager responsibilities, including commercial dealer support and development. Source
Komatsu and Williams Racing reignite historic partnership
Komatsu has signed a multi-year deal with Williams Racing to become the Principal Partner of the British team from the start of the 2024 FIA Formula One World Championship (F1) season. Komatsu was a key partner of Williams Racing in Formula One during the 1980s and 1990s, a period of abundant success for the team. The most notable achievements were in 1996 and 1997, when Komatsu supported Williams Racing to Constructors’ and Drivers’ Championships with Damon Hill and Jacques Villeneuve respectively. Source
John Deere and Leica Geosystems Partner to Bring New Solutions to the Construction Industry
John Deere and Leica Geosystems will collaborate on the development of technology solutions that benefit the construction industry. John Deere SmartGrade™ with Leica Geosystems technology and software will be available for purchase in 2024. The partnership between John Deere and Leica Geosystems will leverage the strengths of both companies to bring new technologies and services to construction professionals worldwide. Source
Read MoreTo see the full list of international logging, roading and trucking conferences and expo’s, please click the “Events” tab at the top of the page.
Read More