“Harvester time consumption in nature conservation management operations”
International Journal of Forest Engineering 2023. Raul Fernandez-Lacruz, Örjan Grönlund, Tomas Johannesson, Line B. Djupström, Jon Söderberg & Lars Eliasson. Source
“Assessment of timber faller working conditions in mixed hand and tethered-machine cut harvest units on steep slopes- A case study in western Oregon”
International Journal of Forest Engineering 2023. Mandira Pokharel, Francisca Belart, Woodam Chung & Brett Morrisette. Source
Read More
Hyundai Doosan Infracore (HDI) Construction Equipment marks a new beginning as DEVELON.
Meaning ‘Develop’ and ‘Onwards,’ DEVELON represents HDI’s new beginning and challenging spirit. The new brand name encompasses their willingness to move onwards to the future through innovation and to change the world with top-level products and solutions.
HDI has a long history of developing products and solutions needed for building infrastructure. Through the years, they have focused on providing products and solutions that exceed the expectations of the industry and our customers. Moving forward, they will introduce more innovative products and solutions that go beyond the world’s expectations.
HDI began their journey in 1937 when they started producing machines. With the new brand name DEVELON, HDI will bring growing momentum with the next leap forward as a global leader in construction equipment products and solutions for building infrastructure.
They have announced a bold name to welcome a new era for their business that encapsulates the core ambition to continue developing onwards and leaving behind a positive footprint in the world
The S5 harvester has been designed to be a pleasure to work in as the ergonomics, space and visibility of the cab have received priority. Operator comfort is further enhanced by automatic cab rotation as well as optional automatic stabilization. Source
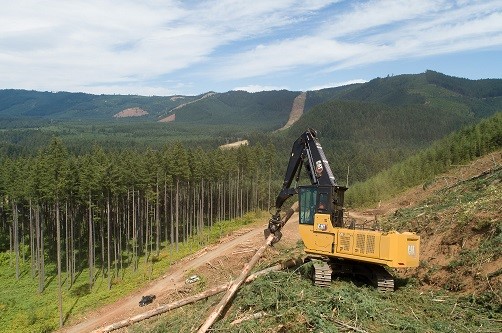
It features several significant design upgrades.
The new 548’s C7.1 twin turbo engine produces 30% more power than the previous series’ engine, enabling the new electrohydraulic control system to deliver 30% more swing torque. Updates to the drive system increase travel speed by 10%, helping the machine cover ground faster than ever.
Smart mode automatically matches engine and hydraulic power to working conditions to help maximise fuel efficiency without sacrificing performance. Cold-start capability of -25˚ F (-32˚ C) and high ambient temperature capability of 126˚ F (52˚ C) enable the machine to work year-round.
The new Certified Forestry cab with its reinforced structure and large 1.25-in (32-mm) thick polycarbonate windshield enhances operator safety. Available in a choice of rear or side entry, the cab’s interior space is 25% larger, allowing most operators to stand without hitting their head. Field of view from the standard heated and cooled seat is 50% better due to narrower cab pillars, larger panoramic windows, and a flat engine hood. A standard rear-view camera enhances visibility as do three available cab risers – 22 in (558 mm), 48 in (1219 mm), and 72 in (1829 mm). The available Cat easy lock cab tilting system on the Log Loader configuration makes for much easier transport.
Ingress and egress are easier due to the cab’s wider and taller door and tilt-up console on the operator’s seat for the side-entry cab. The machine’s new dual HVAC system keeps operators comfortable regardless of working in the summer heat or during subfreezing ambient winter temperatures. Its specially insulated roof and improved window and door seals keep in-cab noise levels low.
Operators can start the 548’s engine with a simple push of a button or available Bluetooth key fob and unique Operator ID. Operator ID allows each operator to quickly program and store their own machine settings and attachment function preferences. A larger 10-in (254-mm) high-resolution touchscreen monitor delivers intuitive navigation through operating menus and includes a digital version of the operator’s manual for quick reference. An available Cat® PL161 attachment locator assists in finding work tools within a range of 200 ft (60 m), even when covered by overgrowth or debris.
Compared to the previous model, the 548 next generation forest machine will consume 50 fewer filters over the course of 12,000 hours, which contributes to lowering maintenance costs by up to 15%. Fuel filters feature a synchronized 1,000-hour change interval – double the service life of the previous model. A new hydraulic oil return filter improves filtration and delivers a 3,000-hour service life, which is 50% longer than previous designs. The high-efficiency cooling fan runs only when necessary, and reversing intervals are programmable to enable the fan to keep the radiator cores clean without interrupting work. Source
JCB’S hydrogen technology set for international debut
JCB is set to showcase its hydrogen combustion technology on the international stage for the first time ever with a debut in North America. The wraps will come off JCB’s brand new hydrogen combustion engine - the company’s zero-carbon emissions solution for construction and agricultural equipment - at the Conexpo 2023 show in Las Vegas as part of the International Fluid Power Exposition (IFPE). Source
Bandit continues to expand manufacturing capacity
With the demand for Bandit products increasing at a steady pace, the need to for additional manufacturing and storage space is a top priority being addressed by the Bandit team. The capacity increase includes Beast manufacturing addition, stump grinder manufacturing addition, a hand-fed chipper manufacturing addition, ship-out / final assembly addition and a new steel processing facility. Source
Katja Paananen appointed Chief Responsibility Officer at Ponsse
She is also a member of the Management Team starting from January 2023. Paananen will report to Petri Härkönen, CFO and Deputy CEO, and her workplace will be in Vieremä. The role of responsibility in Ponsse’s business has grown strongly due to the company’s new strategy and goals, as well as the requirements of our stakeholders. Responsibility guides the company’s future, growth and development. Source
Read More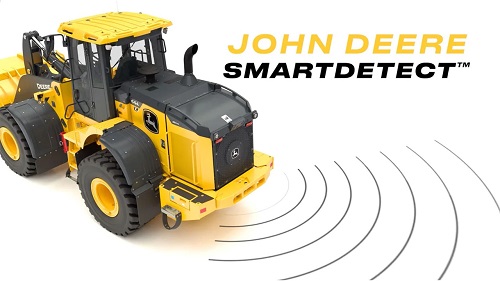
John Deere is exhibiting its latest precision solutions for the construction industry in Las Vegas.
The next generation of John Deere production-class and utility-class loaders are specifically designed to improve operator visibility and awareness. As a direct response to demand from operators, select models can be equipped with new vision and object detection technology. This technology can enhance visibility and help detect obstacles that present jobsite risks.
Object Detection technology, paired with a high-resolution camera and a dedicated display, helps enhance the operator experience and increase situational awareness. In addition, the industry-first vehicle trajectory logic technology overlays the projected vehicle reverse path to illustrate where the vehicle will move next.
Building upon the object detection enhancements, the industry-first Advanced Vision System integrates two digital cameras on the sideview mirror frames, helping to provide increased visibility to the sides of the machine. Within the cab display, operators benefit from an integrated view of all cameras, helping to increase spatial awareness with wider views and enhanced clarity.
The next phase of Deere's technology journey can be found with SmartDetect™ and SmartDetect with Assist. SmartDetect combines cameras and machine learning to help give operators a better view of their surrounds. The system alerts operators when an object enters the machine' projected travel path and provides unique detection alerts for people in the camera' entire field of view. With SmartDetect Assist, the machine will automatically stop before coming in contact with a person.
One of the more advanced technology solutions that will be on display at the show is SmartWeigh, which is now available on the full lineup of P and X-Tier utility wheel loaders and will soon be available on the production-size P-Tier models as well. Aimed to improve cycle times when loading trucks or processing plants, this payload weighing system delivers increased accuracy, dynamic weighing capabilities, and ease of calibration. This John Deere designed-and-supported solution helps operators confidently hit loading targets and minimize material loss. Available fully equipped on loaders from the factory or as a 250-hour trial period, customers that do not typically utilize payload weighing systems can experience the benefits first-hand, helping to prove value and give them the highest levels of productivity on their jobs.
As part of the SmartWeigh system, the dynamic bucket weighing technology eliminates frequent raising and lowering of the boom. The bucket capture height can be set anywhere between 15-90% of boom height and can be captured at any boom speed. Another key feature is that unlike other payload weighing systems, SmartWeigh does not require calibration with a known weight. This enables customers to easily calibrate the system themselves without the need for outside assistance. On top of this, payload weighing data is integrated into JDLink™, meaning it can be accessed nearly anywhere and not just within the cab of the machine.
Also new to the P-Tier and X-Tier wheel loaders, Auto Level technology is designed to eliminate frequent bucket and fork adjustments. Operators moving or handling material do not have to worry about the load tipping too far backwards or forwards as the boom is raised up and down. This feature offers near perfect parallelism throughout the entire raise and lower cycle + or - 2 degrees.
Now standard on the John Deere Small Dozer line-up, with EH controls, is EZ Grade technology, which aids operators in grading smooth finish passes by making small blade corrections automatically. EZ Grade technology is also available on the SmartGrad 333 P-Tier Compact Track Loader, which will be on display at the show.
Also available on the full line-up of small dozers is 2D slope control technology, which helps operators in maintaining flat and sloping grades by automatically controlling the blade to a desired slope. Deere will provide solutions to meet customers where they are today and to grow with them as their grade management needs change. Whether it's EZ Grade, 2D Slope Control, 2D laser, or 3D SmartGrade in the future, Deere small dozers will have solutions for every customer. Additionally, the small dozer line-up is available with a variety of innovative enhancements including larger touchscreen display and the industry trusted John Deere telematics. The data captured, formerly known as JDLink or WITOS FleetView receivers, has been integrated into John Deere's enterprise-wide Operations Center tool. This tool monitors not only machine data but also makes recommendations for a customer's jobsite with things like fuel efficiency in an easy-to-use dashboard view. Customers who have purchased options such as WPT (Wirtgen Performance Tracker) with their machine will also be able to conveniently view this data in the Operations Center in the future. Source
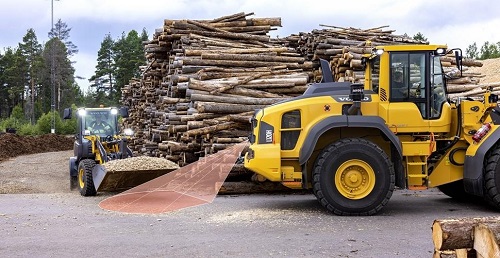
It has an automatic braking feature that supports operator response and helps reduce the risk or consequences of collision when working in reverse.
The first system of its kind from any original equipment manufacturer (OEM), it assists operators while working in reverse and automatically applies service brakes when the wheel loader approaches any obstacle, alerting the operator to take further action. With wheel loaders spending an average of 40-50% of their time being driven in reverse, the Collision Mitigation System is a valuable solution for operators and site managers.
While not designed to ever replace safe operator behaviour, it is a smart tool to further enhance jobsite safety – a central focus and core value for Volvo CE since the company’s inception. As part of the Volvo Group, the company is committed to safety with its Zero Accident Vision which is delivered
With this new system, customers are moving a step closer to not only eliminating accidents – and therefore improving jobsite safety for everyone – but also reducing any unplanned interruptions that can be incurred during those avoidable knocks and bumps.
It works by identifying when there is a risk of collision and responding by automatically activating the brakes for 2-3 seconds to slow the machine down prior to impact or bring it to a stop to avoid it. This initiation of the braking alerts the operator to intervene.
And for seamless stockpiling operations, the system will remember the last slope the machine climbed, allowing operators to reverse down a pile without activating it. It can also be temporarily deactivated for specific site conditions.
Functioning only when the wheel loader is in reverse and driving at speeds of between 3-15 km/h (1.86-9.32mp/h), no matter what gear it is in, it serves as a facilitator to jobsite safety. Even assistance systems like this cannot totally eliminate accidents though, which is why Volvo CE always advocates for safe operator driving behaviour.
Developed in-house by Volvo CE, the patent-pending Collision Mitigation System for Volvo Wheel Loaders is a factory-fit option currently available on the L110H/L120H equipped with OptiShift, L150H, L180H, L220H, L260H and L200H High Lift wheel loaders.
Requiring a Radar Detect System to be fitted, it works as an additional system to the existing wide range of features, options and site services provided by Volvo CE for its line of wheel loaders, all of which have been designed to elevate jobsite safety and minimize unplanned interruptions. Collision Mitigation System is available in all markets around the world. Source
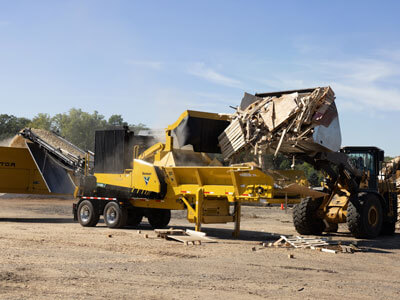
It is sized for tree care professionals and mulch producers.
This new generation of the HG4000 delivers powerful performance in various wood waste recycling applications and landscaping material production. It’s equipped with a 536 hp (400 kW) CAT C13B T4F/Stage V diesel engine, a Series III duplex drum, an aggressive infeed to accommodate a variety of materials, and many performance and durability features. It’s quiet, too, with a working sound level of 112 decibels.
The Vermeer HG4000 horizontal grinder is ideal for professionals looking to expand their service as well as for bulk landscaping material producers. It’s great unit for turning waste into a useful end product. It’s also a productive machine for small to midsize mulch producers with limited space for the material. The size of the HG4000 also makes it efficient to transport in congested urban environments making it an ideal machine for small land-clearing operations. And while this horizontal is smaller than other machines in the Vermeer grinder product line, it still can handle a variety of materials ranging from loose, bulky materials like leaves, branches and yard clipping to hardwoods, pallets and logs.
The HG4000 has a feed table capacity of 4.6 yd3 (3.5 m3). It features the cutting performance of the Vermeer patented Series III duplex drum with reversible hammers and tips for extended wear life compared to single- sided designs while offering bolt in replacement parts. The hard-faced anvil on the HG4000 delivers impressive cutting action with the drum, and a redesigned robust anvil-mount structure helps ease the hard-faced wear edge replacement process.
The HG4000 benefits from an updated feed roller with aggressive teeth and down pressure to maintain control of the fed material. A fully enclosed feed roller drive planetary helps provide protection and a tight clearance between the roller and mill housing to optimize material feeding while minimizing material catch points.
A wireless remote control comes standard with the HG4000, allowing operators to run most machine functions from up to 300 ft (91 m) away. With the remote, operators can adjust infeed settings, engine speed droop, conveyor height and more, which means maximum time grinding throughout the day.
The redesigned Vermeer HG4000 incorporates several service and maintenance enhancements, including a drive belt tensioning system that does not require the engine to be moved when adjusting, large hinged side shields for optimal maintenance access, added power rotation to the screen hoist for changing screens, and a CAT engine with worldwide support. It can also be outfitted with an optional cross-band magnet and magnetic head pulley to pull metal from the top and bottom of material on the conveyor after it has gone through the machine for clean finished material.
The HG4000 has a transport width of 8.2 ft (2.5 m), a height of 13 ft (4 m), a fifth-wheel hitch trailer length of 32 ft (9.7 m), and a weight of 52,910 lb (24,000 kg), or a pintle hitch trailer length of 37 ft (11.3 m) and weight of 55,155 lb (25,000 kg). Source