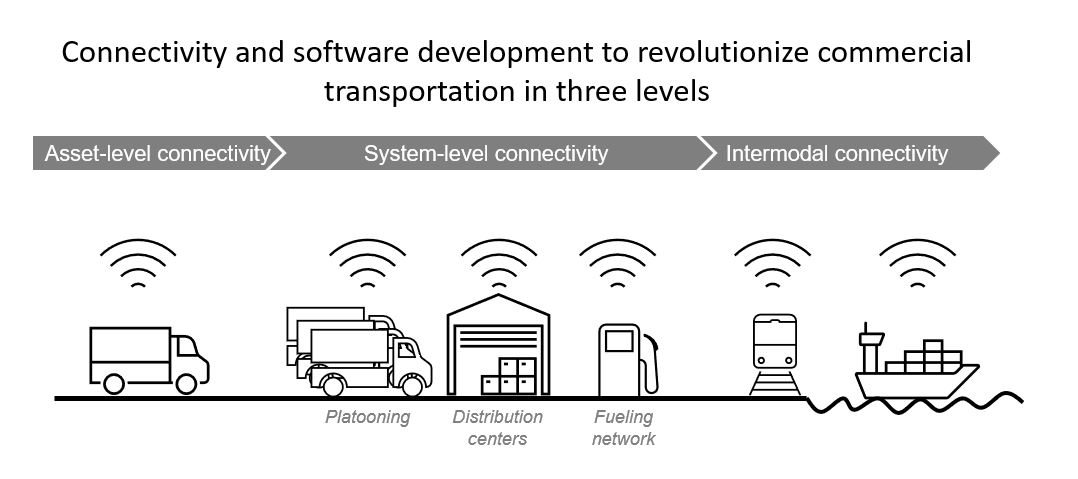
Advanced technology will pave the way to exceed what was previously thought possible.
The commercial transportation industry faces rapidly changing regulations and evolving customer needs. Cummins examines the future of commercial transportation, and indicates that it will be shaped by three perspectives: a shifting energy mix, innovations in software, and evolving use cases driven by autonomous driving and vehicle-as-a-service (VaaS). This is the second part of this Cummins provided article. The first appeared in the July 2 Newsletter of Logging-on.
The commercial transportation sector has already begun a rapid period of software development, helping fleets avoid accidents, optimize their fuel usage, and identify the best routes. Going forward, safety will continue to be paramount; meanwhile, connectivity and software development will revolutionize condition monitoring and performance optimization. This revolution will take place at three levels: asset-level, system-level, and intermodal.
In the near future, asset-level connectivity will continue to be under a spotlight. For example, Cummins is already testing prognostic algorithms that leverage massive amounts of data to move customers away from reactive service models to predictive, planned maintenance. The idea is this: sensors in the vehicle monitor the way equipment is performing and report abnormalities. This allows us to detect potential issues early enough that the necessary action can be taken, either through over-the-air updates or at the next scheduled maintenance, so unplanned downtime is reduced, increasing the availability and reliability of the equipment.
Soon, we will see an increased focus on system-level connectivity, where emphasis will expand to managing the complete fleet and system elements such as distribution centers and refueling stations. With this, we will see the sector continue to drive automated decision making through an increased reliance on harnessing real time data and computing capabilities.
Finally, intermodal connectivity will connect different modes of transportation. This will create a commercial transportation eco-system where individual assets among different modes of transportation such as road, rail, sea, and air are connected and operate in harmony.
One of the things common between autonomous trucking and VaaS (Vehicle as a service) is they may both drive an evolution among commercial transportation use-cases, but at different scales.
Autonomous trucking may have more profound impact on transportation, as more vehicles start to communicate with each other and with infrastructure elements such as traffic signals and depots. A key outcome of the rise of autonomous trucking could be the competitiveness of trucking against other modes of transportation such as rail. Autonomous trucking could also impact the financials of the industry; as these vehicles will be highly utilized, which could lead to shorter replenishment cycles and lower volumes of vehicles to own. As the safety considerations are getting addressed, this and the increasing focus on system-level connectivity will also continue to shape the role of the drivers in autonomous vehicles.
Vehicle-as-a-service, on the other hand, may have a limited impact in commercial transportation. VaaS, which mirrors the efficiency model used by Uber and Airbnb, primarily relies on under-utilized assets. Meanwhile, commercial transportation is inherently different from privately-owned cars and homes, where a wealth of these under-utilized assets exists. In commercial transportation, there is not a large reserve of under-utilized assets. Therefore, the impact of VaaS in commercial transportation could be limited to two areas. Firstly, fleets with under-utilized vehicles could see improved efficiencies with VaaS. Secondly, VaaS could also find traction with fleets where access to financial resources is limited. In these use cases, the increasing cost of vehicles, due to a combination of decarbonization, advanced connectivity and autonomous features, could make it more difficult for fleets to spend high capex upfront. For these fleets, VaaS could be the more economically-viable path forward. There may also be use-cases where a combination of VaaS and advanced autonomy (without a driver) could address chronic driver shortage issues. Meanwhile, for fleets where utilization rates are already very high and access to finances is not an issue, the impact of VaaS will be limited.
Commercial transportation is certainly in a period of rapid change, but the sector has always pushed hard to ensure it would meet the needs of society. Today, those needs are increasingly demanding, and technology will once again rise to the challenge. Source
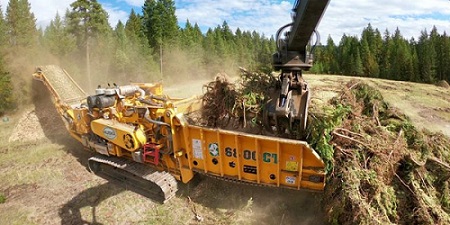
These hold the potential to revolutionize the way we produce and consume energy.
In today's rapidly changing world, the search for sustainable and renewable energy sources has become more critical than ever. With concerns about climate change and depleting fossil fuel reserves, innovative solutions are needed to power our planet's future.
Biomass energy harnesses the power of organic matter, such as plants, wood, and agricultural waste, to generate heat, electricity, and even biofuels. It offers several significant advantages over traditional fossil fuels, making it an attractive and environmentally friendly alternative. Advancements in biomass conversion technologies have played a pivotal role in maximizing energy output while minimizing waste.
Traditional biomass energy systems primarily relied on agricultural crops, such as corn and sugarcane, as feedstocks for biofuel production. However, ongoing research and development have expanded the range of available feedstocks, making the process more sustainable and less prone to competition with food production. Today, biomass feedstocks include various types of plant matter, wood residues, algae, and even waste materials. This diversification not only ensures a more abundant and reliable energy supply but also reduces the strain on valuable agricultural land.
While first-generation biofuels have made significant contributions to the renewable energy landscape, second-generation biofuels are emerging as a game-changer. These advanced biofuels are produced from non-food feedstocks, such as agricultural residues, forestry waste, and dedicated energy crops. The use of these feedstocks minimizes the carbon footprint associated with biofuel production and mitigates concerns about food scarcity. With ongoing advancements in biofuel refining techniques, second-generation biofuels are becoming increasingly cost-effective and commercially viable.
Another exciting development in the biomass energy sector is the concept of integrated biorefineries. These facilities go beyond simple energy generation by utilizing a holistic approach to biomass utilization. Integrated biorefineries combine multiple conversion processes to produce a range of valuable products, including biofuels, biochemicals, and bioplastics. By extracting maximum value from biomass feedstocks, these refineries create a sustainable and economically viable model for the future.
One of the most significant advantages of biomass energy lies in its ability to address waste management challenges. Organic waste, such as agricultural residues and food scraps, can be transformed into useful energy through anaerobic digestion or thermal processes. This not only reduces the environmental impact of waste disposal but also creates a valuable resource. By diverting organic waste from landfills, biomass energy helps mitigate greenhouse gas emissions and prevents the release of harmful pollutants into the environment. Additionally, the byproducts of biomass energy production, such as nutrient-rich digestate from anaerobic digestion, can be used as fertilizers, closing the loop on nutrient recycling and promoting sustainable agricultural practices. Through sustainable waste management strategies that incorporate biomass energy, we can minimize waste, conserve resources, and contribute to a cleaner and healthier planet.
The advancements in biomass energy and biofuels discussed in this article represent just a glimpse of the potential that lies ahead. With ongoing research, technological breakthroughs, and collaborative efforts, we can continue to refine and expand the applications of biomass energy, making it an increasingly viable and widespread solution to our global energy needs.
CBI is one of the organisations that is providing optimal solutions. It all starts with CBI’s unique offset-helix rotor. Based on the principles of kinetic energy, the heavy-duty rotors require less power to rotate continuously, while aggressively outperforming other rotors in terms of throughput. The optimized design of CBI’s heavy-duty anvils, screens, hammer configuration and cutting angles work in concert to deliver a superior cutting process and highest-value end product. This can, for example, be leveraged by manufacturers of wood pellets (when the feed stock is logs) because it eliminates costly phases of their manufacturing process. A single pass through a CBI biomass chipper can yield short-chip (micro-chip) material that doesn’t need to go through the initial hammermill process before entering the dryer. The eliminated process greatly reduces power consumption and emissions. Source
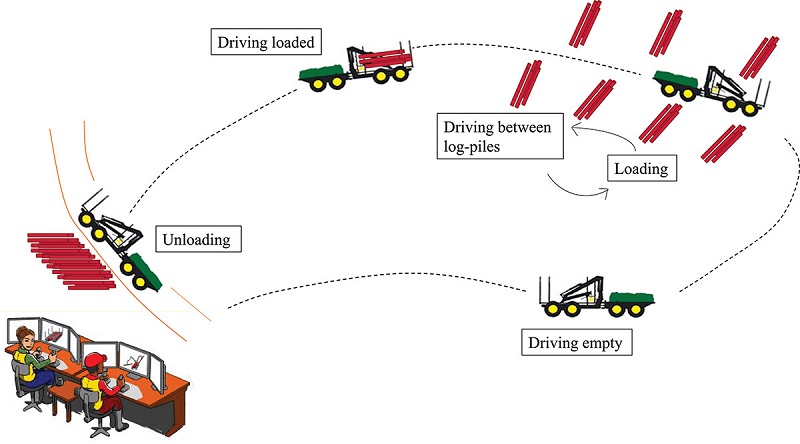
Fuel consumption affects both costs and environmental impact of logging operations.
Traditionally, fuel consumption has been estimated through studies of individual machines, through follow-up studies based on company records or through questionnaires. Using automatically collected data from machine computers, in the form of standardized harvester production, forwarder production, and machine operational monitoring files, offers a new way to estimate fuel consumption. Researchers aimed to estimate fuel consumption in cut-to-length logging operations based on automatically recorded data, and to evaluate whether this data is sufficient on its own or needs to be supplemented with additional data.
Average fuel consumption per harvested m3 varied from 1.4 to 3.4 l (0.31 to 0.75 gal), depending on machine size, tree size, and transport distance. The study shows that fuel consumption per machine type or logging team can largely be explained using the machine data. Classification of machines into size classes is a challenge, as machine configurations vary between individual machines, but such classification may not be needed. Forwarded volumes are a source of error, since this data is manually fed into the machine computer and, therefore, often deviates from the felled volume in a harvesting block. This will probably cause a slight overestimation of forwarder fuel consumption.
Estimating fuel consumption based on automatically collected data from the machine computers, in the form of standardized harvester production, forwarder production, and machine operational monitoring files, produces reliable results. Fuel consumption per m3 varied from 1.4 l (0.31 gal) for teams with a large forwarder to 3.3 l (0.73 gal) for teams with a small forwarder. These results compare well with results from studies using more traditional methods. A source of variation that needs to be addressed is inaccuracies in the manually reported forwarded volumes. Better classifications of the machines used might improve the results – but the results indicate that machine classifications might be unnecessary – as would better descriptions of the work task.
This information was published in the International Journal of Forest Engineering (2023). The title was “Fuel consumption in logging operations in Sweden” and the researchers were Eliasson, Kalle Kärhä & John Arlinger. Source
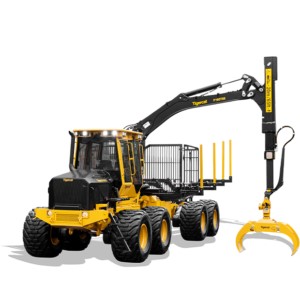
The automation of crane work and teleoperation of driving of a forwarder was modeled and simulated and showed potential cost savings.
Within cut-to-length forwarding, a theoretical semi-autonomous teleoperation concept called tele-extraction, with automation of crane work and teleoperation of driving, was modeled and simulated. Both configurations modeled had greater potential for cost reduction than a previously studied alternative where the driving was automated, and crane work was teleoperated. Teledrive with teleoperated driving empty, driving loaded, and driving between log piles while loading, showed a reduced cost of 10% for five operators on ten forwarders, whereas teledrive with both loading and driving while loading automated showed a reduced cost of 18% at four operators. In both configurations, the lowest cost was reached at about 10% lower productivity compared to standard forwarding. Increased extraction distance had a negative impact on potential for cost reduction since the driving was teleoperated while terminal activities were autonomous.
Teledrive in different variants has the theoretical potential to be up to 18% more cost efficient than standard forwarding; and, as opposed to the previously studied tele-extraction configuration, the potential for teledrive was largest for short extraction distances since that is what results in the highest share of autonomous work during a forwarder load cycle. Sensitivity analyses of changes in operator cost, changes in time consumption for autonomous work, increased payload, and extra waiting times resulted in a variation of the theoretical potential between 3 and 24% cost reductions. The absolute maximum potential cost reduction from automation, so-called Full Auto based on equal time consumption for the same work elements, was 38%, corresponding to removing the operator cost completely.
This information was published in the International Journal of Forest Engineering (2023). The title was “New configurations of the tele-extraction concept” and the researchers were Mikael Lundbäck, Carola Häggström, Dag Fjeld & Tomas Nordfjell. Source

Researchers examined the potential of hybridized drivetrains for tower yarder applications.
Radical changes are necessary to address challenges related to global warming and pollution. Ever-tightening emission standards for combustion engines have already led to a drastic reduction in the amount of harmful gas and matter emitted. Drivetrain hybridization and electrification, which are becoming increasingly popular in all sectors, are two additional ways to achieve that goal. However, within the forestry sector most of the equipment still rely on conventional mechanic or hydraulic drivetrains. An example of this is tower yarders, the workhorse of the alpine logging industry.
This research simulated the duty cycle and energy flow of tower yarders in logging operations, both with conventional diesel–hydraulic configuration and a proposed hybrid configuration. The objective was to determine the potential of hybridized drivetrains for tower yarder applications. Detailed models were developed to describe the cable-based extraction of timber and tower yarder internal processes. Extensive simulations were performed to determine force, power and energy components during the harvesting operation for both the diesel–hydraulic and hybrid drivetrains.
Results confirm the large potential of the hybrid configuration for efficiency improvement and emission reduction, with estimated fuel savings of 45% and 63% in the uphill and downhill configurations, respectively. Extensive sensitivity analysis further demonstrates that the hybrid concept remains effective across a wide range of cable setup and transport characteristics. This confirms the large potential of electrified drivetrains, especially in the presence of very dynamic duty cycles, as is the case in cable-based logging equipment.
This research was titled " Tower yarder powertrain performance simulation analysis: electrification study” and was published in the European Journal of Forest Research. The researchers were Stefan Leitner, Manuel Antonio Perez Estevez, Massimiliano Renzi, Raffaele Spinelli, Fabrizio Mazzetto & Renato Vidoni. Source
Ponsse and PacWest sign a retail agreement for the West Coast of the United States
The Ponsse Group has signed a retail agreement with PacWest Machinery in the United States. At the same time, the companies have signed a deed of sale according to which Ponsse sells its service business operations in Coburg, Oregon, to PacWest. In the future, PacWest will be responsible for the sale and maintenance of Ponsse forest machines in the states of Oregon, Washington and Idaho on the West Coast of the United States. Source
Hypro introduces a new "Drive" option for the 755 HB wheel carried processor
With the new Drive option for the Hypro 755 HB wheel carried processor, driving on steep uphill’s is no longer a challenge. The new solution consists of two different options (G-Drive and Hub-Drive). With the G-Drive, the wheel easily climbs over obstacles, whereas in the past the tractor would have stopped. Source
Log Max have a new dealer in Denmark
MP Maskinteknik now serves and sells Log Max harvesting heads in Denmark. They have extensive experience as service technicians. Source
Read More“Forest damage and forest supply chains: a literature review and reflections”
International Journal of Forest Engineering, 2023. Anders Roos. Source
“New configurations of the tele-extraction concept”
International Journal of Forest Engineering, 2023. Mikael Lundbäck, Carola Häggström, Dag Fjeld & Tomas Nordfjell. Source
Read MoreTo see the full list of international logging, roading and trucking conferences and expo’s, please click the “Events” tab at the top of the page.
Read More